Release date: 2016-08-01
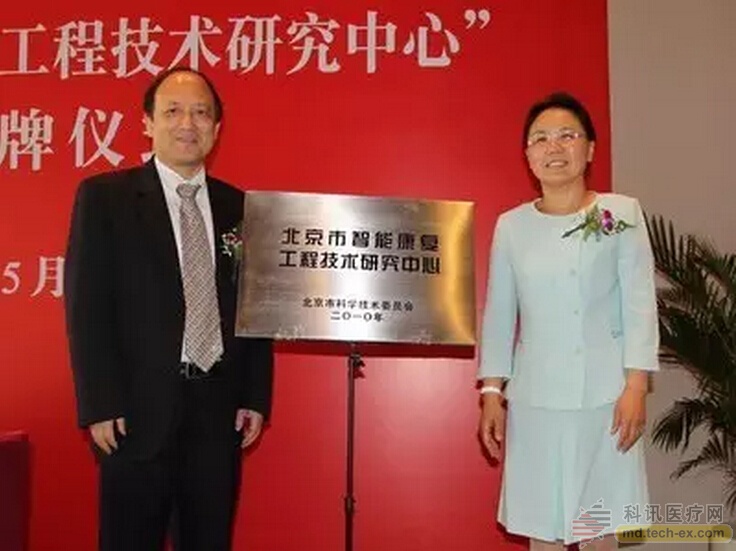
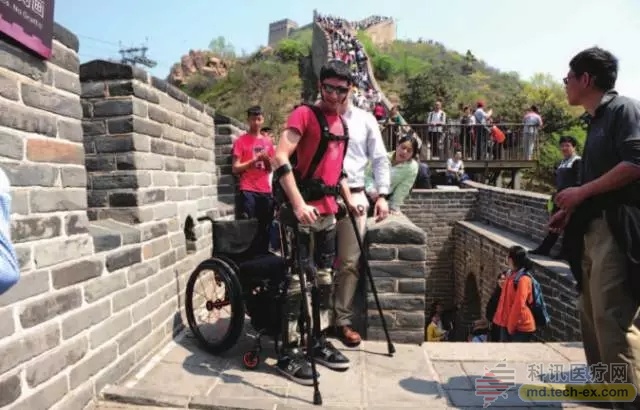
"Financial" reporter Lu Fangrui / text
At the corner of Peking University campus, the Beijing Intelligent Rehabilitation Engineering Technology Research Center is located. Engineer Zhou Yalei is sitting in the middle of a pile of boxes and is trying to assemble several custom parts. On the shelf behind him, there is a robot, the upper body is like a backpack, and the lower body is two mechanical legs. This is their latest development of exoskeleton robots.
Robot is a robotic device that performs work automatically. It can accept human command, run pre-programmed programs, or act according to the principles of artificial intelligence technology to assist or replace human work.
The exoskeleton robot that Zhou Yalei is making is to help the paralyzed patients walk. The patient puts the upper part of the device on his back and the mechanical leg is tied to the outside of the legs. With the support of the mechanical structure and the operation of the motor, the patient can stand up again.
The Global Burden of Disease estimates that approximately 975 million people (19.4%) worldwide have disabilities. About 190 million people (3.8%) have “severe disabilities†– such as quadriplegia, severe depression or blindness.
Rewalk, Ekso and Cyberdyne are pioneers in the field of medical exoskeleton robots. There are also research institutes such as the University of Electronic Science and Technology, the Institute of Advanced Technology of the Chinese Academy of Sciences and the Peking University. They hope that medical treatment will be used to bring exoskeleton robots to more patients.
If you can really let all the paralyzed patients stand up again, it is undoubtedly an epoch-making feat. But before completing this task, the exoskeleton robot must solve its own technical problems.
Walking patient's walking dream
Lin Han, 24, accidentally fell from the fourth floor in 2013 and caused spinal cord injury. His lower limbs lost their athletic ability.
Lin Han told the Caijing reporter that he had tried to get rid of the wheelchair many times, but his knee could not support his body weight. He tried traditional rehabilitation training such as acupuncture and strength training, and the effect was not good.
In 2015, Lin Han met the exoskeleton robot developed by the University of Electronic Science and Technology in the Bayi Rehabilitation Center in Sichuan Province, and immediately became a tester.
The exoskeleton robot was first developed in 1965 by the United States General Electric Company and the US military, with the intention of assisting soldiers in military activities and enhancing the ability of soldiers to carry heavy loads. Later, a number of commercial companies and research institutes changed their research direction and developed medical exoskeleton robots that help paralyzed patients walk.
Exoskeleton robots drive the patient to walk and require coordination of the various parts.
First, the exoskeleton robot captures the patient's walking intent through the sensor. "Some products use a tilt sensor that monitors the body's forward tilt and uses subtle changes in the center of gravity to control motion." Professor Cheng Hong, executive director of the Robotics Research Center at the University of Electronic Science and Technology, told the Caijing reporter.
Then, the exoskeleton robot will run the motor at the joint, and the motor drive link will take the steps of the person's legs. A powerful motor can drive the patient to walk, and the patient only needs to balance with both hands and crutches.
In order to make the patient walk more naturally, the engineers divide the walking posture into several stages, such as the standing state of the legs, the dynamics of the left leg swing and the dynamics of the right leg swing, and set the motor parameters according to the movement characteristics of each stage. Make the walking posture of the mechanical legs closer to people.
As the pace progresses, the patient holds the crutches in both hands and alternates with the foot to maintain the balance of the body. After a period of adaptive exercise, many patients can walk more skillfully. “Lin Han can be mastered in only one or two months,†said Huang Rui, a doctoral student at the Institute of Machine Intelligence at the University of Electronic Science and Technology.
The mechanical skeleton of the exoskeleton robot uses a high-strength alloy material that supports most of the weight of the patient's body.
In many low- and middle-income countries, public services such as health care and rehabilitation are severely lacking, and there are few barrier-free facilities in public places. Even small people who take things from the shelves and go to the toilet alone will become huge challenge.
The long-term wheelchair and bed career also brought them a variety of diseases. Medical research has confirmed that the long-term bedridden paralyzed patients have reduced respiratory volume, coughing action is weakened or disappeared, respiratory secretions are not well discharged, and pulmonary infection is easy to cause; sputum patients lack long-term exercise, which may cause joint rigidity, muscle atrophy and thrombosis; Osteoporosis can be caused by factors such as the disappearance of muscle contraction on the bone and changes in the patient's calcium-regulating hormone.
Therefore, it is a great thing to let these patients stand up and do some trivial things in their daily lives.
A few months after being a trial of exoskeleton robots, Lin Han wore an exoskeleton robot and completed the torch relay mission of the Ninth National Paralympic Games.
Price, weight and ease of use are difficult to balance
Lin Han has been able to use the exoskeleton robot activities, but he still feels that the device on his body is a bit heavy, reaching 21 kg. Researchers such as Huang Rui and Zhou Yalei also admitted that most of the equipment on the market, including their products, weighs several tens of kilograms, and that patients can't wear them for a long time. They need to wear and remove equipment frequently when getting on and off the wheelchair.
"This is already the lightest and smallest motor that can be bought," Zhou Yalei told the reporter of Caijing on the motor of the exoskeleton knee. "The weight of the battery is also limited by the current technology, and there is no way to reduce it."
Many research teams in China focus on the design of mechanical structures and the development of control systems. Motors, sensors and other accessories are purchased from professional manufacturers. “We try to reduce the weight on metal materials. These custom parts use the lightest alloy materials on the market.†Zhou Yalei said.
The main difficulty of exoskeleton robots is lightweight. This depends on the development of many related technologies, such as the weight reduction of motors and batteries. "We hope to eventually make a product that is as easy to wear as glasses," Huang Rui said.
Another technical difficulty is how to keep the exoskeleton robots self-balancing. Most of the products on the market today cannot be done, and the patient needs to support the walking stick with both hands, which limits its scope of application.
Goffer, the inventor of Rewalk, couldn't use Rewalk himself because he was paralyzed. "Not all medical exoskeletons have conditions for self-balancing. Most of them only drive the wearer's knee joints, which do not completely affect the wearer's lower limb movements, and cannot achieve self-balancing." Ouyang, Associate Professor, School of Mechanical Engineering, Zhejiang University Xiao Ping told the Caijing reporter.
The self-balancing of the exoskeleton means that the robot is able to determine whether or not instability has occurred and to be able to exercise control of its mechanical limb (along with the wearer's limb).
The weight of the upper body of the human body has a greater influence on the position of the center of gravity. To achieve self-balancing, the exoskeleton needs to be able to observe the weight distribution including the upper body of the human body. However, this is beyond the scope of the medical lower extremity exoskeleton robot.
In motion control, the medical exoskeleton works by driving the patient's limbs in accordance with the set gait, thereby assisting the patient to resume walking. However, in order to maintain the self-balancing instability control, it is required to adjust the gait in real time, contrary to the use requirement of walking according to the preset gait.
To master the use of exoskeleton robots, patients also need long-term training. The US Department of Veterans Affairs purchased multiple Rewalks to help injured and rehabilitate injured soldiers. Dr. Spangen, deputy director of rehabilitation research at the department, said that it takes time to adapt to exoskeleton robots. And not all paralyzed patients can complete the Rewalk training, and some people can't learn it.
It is not impossible to solve one or both of the above problems, but at the current state of the art, it is difficult for exoskeleton robots to balance price, weight and ease of use.
The materials provided by Cai Dengboge, who is responsible for public relations affairs at SuitX, to the Caijing reporter show that their products greatly simplify the mechanical structure, reduce the manufacturing cost and reduce the weight; the joint parts can be opened and used separately, sold and supplied to Healthy people with physical labor have increased sales and shared R&D costs.
However, this comes at the cost of reduced ease of use.
Huang Rui believes that in order to reduce costs and reduce weight, this equipment sacrifices the natural nature of gait and removes functions such as going up and down stairs. Patients need to spend more time practicing to become proficient with the product.
Lin Han and the Electronics Science and Technology team hope that the technology upgrade will solve the above problems. During the experiment, Huang Rui's team found that most of the applications had low requirements on motor power, so the next generation of products they were developing chose a smaller power motor and simplified the mechanical structure.
These two changes are expected to result in a weight loss of 7 kg. According to the needs of different patients, the product customization method can be used to cancel some redundant functions and structures, and the price and ease of use can be considered to some extent.
However, considering the functionality and ease of use, at the current state of the art, weight and price can only be balanced.
How to sell
Lin Han has recently been busy helping the team collect usage data, writing manuals, and helping teams improve their products. He expects the next generation of products to allow him to walk more freely. How to get more people to get a walk, you need to consider how to commercialize laboratory products.
Since most of the domestic related research is aimed at scientific research, there is a general lack of commercial consideration in the early stage of the project. Therefore, the marketization rate of domestic R&D products is significantly lower than that of foreign companies.
“We are working with medical institutions to provide products for free to patients. At the same time, our products are also undergoing certification procedures. After certification, products can be sold.†Cheng Hong said.
Certification of exoskeleton robot products is a key step in commercialization.
As a medical device, the domestic medical exoskeleton robot should apply for certification from the State Food and Drug Administration (hereinafter referred to as the Food and Drug Administration). Because the product is at the forefront, there is no specific standard. The Food and Drug Administration must first classify it, then carry out inspections, clinical tests, and finally certification.
The researchers are waiting for the classification results of the Food and Drug Administration. At present, no domestically produced products have passed the certification. The Cheng Hong team is the first team to enter the certification process.
In clinical trials, they found that the commercialization of domestic exoskeleton robots is difficult to dispel the safety concerns of patients. Many patients have long-term lack of exercise and the lower limbs are unaware. When they use the product, they feel like the body is floating in the air, there is no sense of security. However, after a month or two of training, the patient's lower limbs slowly return to consciousness, and the exoskeleton robot can be consciously controlled, and the safety concerns can be eliminated.
Even after passing the certification, the sales of domestic and foreign products that have already been listed are still not satisfactory.
Rewalk is the first exoskeleton robot certified by the US Food and Drug Administration (FDA). Throughout 2015, its manufacturer Rewalk Robotics had a total operating income of $3.746 million. Even if the revenue is fully converted, Rewalk sold only 50 sets last year, based on the price of $70,000 per device.
According to the US Center for Disability Statistics, more than 6.8 million US residents are using assistive equipment, including 1.7 million patients using wheelchairs or scooters, and 6.1 million users using other mobile devices (such as crutches, canes, etc.).
There is a sharp contrast between sales and the sheer number of patients. "There is also a exoskeleton that can be self-balancing, called REX. Of course, the cost of self-balancing is very large. First of all, it needs to be very large in structure because its joint structure is more complicated. Secondly, it is on the control algorithm. There are also high requirements. These products are bulky and expensive, and there is no advantage in the market." Huang Rui said.
Expensive, because of the high manufacturing costs. Alloy materials, which are manufactured in irregular shapes, require custom motors, which increase costs. According to Huang Rui, the motor used by the exoskeleton robot they developed is a few thousand dollars. A set of exoskeleton robots, the cost of only the motor and custom parts will reach about 100,000 yuan.
REX sells for about $150,000; Rewalk, which has a simpler structure and lower cost, sells for about $70,000; the lowest price on the market is the "Phoenix" from SuiteX, which costs about $40,000. The price of domestic products is more advantageous.
In terms of materials, both domestic and foreign are purchased industrial products, and the cost is not much different. Domestic products are exempt from customs duties, and they are more dominant in research and development costs such as personnel costs. Cheng Hong revealed that after their products are listed, the price is expected to drop below 200,000 yuan.
However, such prices are still unaffordable for the average person, not to mention that most of the deaf patients do not have a job income. Li Wei, who is engaged in the promotion of medical devices, told the Caijing reporter that he is optimistic about the prospects of exoskeleton robots, but at present the products are too expensive, he does not consider getting involved.
This is back to the old problem, how to achieve the price, weight and ease of use, allowing most patients to use a suitable product, the need for researchers and the market to work together.
(The first issue of this article was published in the July 25, 2016 issue of Caijing magazine)
Source: Financial Journal
Chewable Tablets,Vitamin C Chewable Tablets,Chewable Vitamin C,Chewable Calcium
Guangzhou Etechange Biological Engineering Co.,Ltd. , https://www.etechange.com